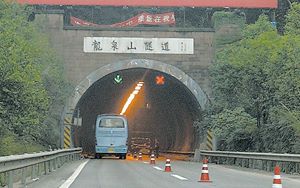
历时3年半,成渝客专新龙泉山隧道在4月30日全线贯通,为2015年实现全线通车奠定了坚实基础。成渝两地迈入1小时经济圈指日可待,同时作为沪汉蓉快速客运通道的重要组成部分,成渝客专也将成为四川重要的高铁出海通道。
应战“高瓦斯”
新龙泉山隧道全长7.3公里,是全线的重难点控制性工程,也是目前四川省最长的高铁双线隧道。隧道横跨龙泉山断层,地质相当复杂,其中Ⅳ级围岩4.7公里,Ⅴ级围岩1.1公里。隧道穿越浅层天然气、断层破碎段、节理裂隙密集带等不良地质地段,其中高瓦斯区段接近2.7公里。1号斜井坡度达38.2%,2号斜井坡度达37.9%,在国内同类隧道中亦属罕见。开挖过程中还有突水突泥、反坡排水等难题,掌子面单位时间最大涌水量为2.2立方米/分钟。由于地质情况恶劣,新龙泉山隧道被中国铁路总公司评估为极高风险的高瓦斯隧道,是成渝客专全线最难啃的一块“硬骨头”。
2010年9月,项目部组建进场,着力优化施工组织设计方案,加强施工管理,大力推进安全教育常规化,制度落实责任化,现场施工标准化,施工管理精细化,监控量测信息化。高瓦斯隧道施工的安全是重中之重,项目部建立并严格实施了岗前安全培训制度、超前地质预报制度、瓦斯监控制度、围岩量测制度等,做好隧道通风,完善应急预案体系,以确保施工安全万无一失。同时,要求现场严格落实工序实名制、三员带班制、封闭管理制、进出洞实名制等,并积极采用诺姆特喷射机械手、仰拱移动模架等新设备,应用湿式喷射混凝土新工艺,保证施工质量、安全和进度。
2010年10月,隧道正式开工。施工初期,由于地质松软、高瓦斯、高危岩、大跨度、大变形、浅埋深等复杂地质条件,施工一度受困,特别是在地质条件最恶劣的近80米的断层破碎带,支护过后不断产生变形,项目部多次组织专家和设计单位对施工方案进行研究,提出采用“三台阶,七步开挖”的方法,按照“短开挖、强支护、早封闭”的原则,快速安全地通过复杂地质段。在进口的掘进过程中,采用CRD法、加大拱脚法、侧向大管棚加固、地表注浆夯填等进行处理和尝试,采用多种加固措施,终于稳定了围岩。
新龙泉山隧道内的瓦斯蕴含在岩石缝隙中,施工时瓦斯在隧道内聚集,如果瓦斯浓度超过一定阈值就会造成燃烧、爆炸或致人窒息,后果不堪设想。为确保安全,项目部委托专业机构负责施工期间的瓦斯防治技术,并形成了由瓦斯监控系统、专职瓦检员检测、管理人员及其他特殊工种人员检查三部分组成的瓦斯检测体系。同时将整个隧道划分为4个区域,每区安装1套瓦斯监控系统,同时装备“风电闭锁、瓦电闭锁”功能,并根据规范设置瓦斯监控系统的报警、断电、复电门限瓦斯浓度,在每个洞口配3名瓦斯监测工,采取三班作业,实行24小时值班维护制度。
项目部常务副经理王银之说,施工人员进入隧道前都要通过安检门,确保没有带打火机、手机或其他电子设备,杜绝一切火源;进入隧道的人员也不得穿化纤衣物,因为化纤衣物易摩擦产生静电,静电则可能引发瓦斯爆炸。
渣料有轨运输
由于是瓦斯隧道,坡度太大,空间狭小,无法采用常规的无轨运输,近40万立方米的弃渣和近11万立方米的混凝土运输成为一个令人头疼的难题。项目部集思广益,多次召开研讨会,最终决定引进矿用提升机进行有轨运输,解决了大坡度斜井瓦斯隧道不能无轨运输的难题。
进入正洞和平导施工后,出渣和进料都需要经过两次转换、三次运输。以运渣为例,要先通过梭式矿车将掌子面的渣料运送到斜井井底,卸渣后装入侧翻矿车,再通过有轨运输传送到斜井井口自动翻渣,最后通过无轨运输送到弃渣场。为了提高工效、降低成本,项目部把工序衔接作为重点,在1号斜井井底设置井底翻渣平台,提高储渣能力,合理布置有轨运输轨道,合理配置矿车数量,缩短工序循环时间,加快施工进度。同时,设置专人每天对绞车系统和运输轨道进行检查、维修和保养,发现问题及时处理,以保证设备性能、轨距、线型、道岔、枕木、连接位置正常。每次循环作业时,专业铺轨人员在开挖完成后,还要及时接长钢轨和移动仰拱栈桥,快速保质保量打通运输通道。
创新格栅钢架加工
在格栅钢架加工过程中,由于当时市面上无四肢格栅钢架加工设备,原有自制加工设备无技术突破,多数施工单位一直沿袭传统加工方法,只能制作“八”字筋,不能按照设计图纸要求制作“8”字筋,既造成了焊材浪费,也满足不了图纸设计要求。为此,项目部组成了技术攻关小组开始艰苦的攻关工作,查阅资料、电脑检索、向一线工人请教加工难题、每周召开技术会进行交流和总结、现场加工试验……最终,充分考虑到立体弯曲后的尺寸变化,按设计“8”字筋尺寸下料,然后采用弯曲机按尺寸制作成“回形针”形,再利用自制平面液压加工设备加工“回形针”成“8”字形,并按设计要求焊接,最后采用竖向液压加工设备竖向挤压成立体“8”字筋结构,并按设计要求焊接在模具中的主筋上。这种加工方法制作步骤操作简单,不但提高了加工速度,加工质量也更容易控制,在节约焊材的同时,钢架整体性比原来更好,强度更高,该项创新获得了国家专利。
新龙泉山隧道的施工过程中,项目部先后成立了多个现场科技攻关组,分别对洞口翻渣平台优化、大角度相交轨道运输安全、通风方案调整、仰拱移动模架浇筑仰拱混凝土、悬臂吊车吊装作业等进行科技攻关,不但解决了实际问题,提高了生产效率,而且提高了项目管理人员的创新意识和技术水平。